Accueil
L'avenir ne se prévoit pas, il se prépare
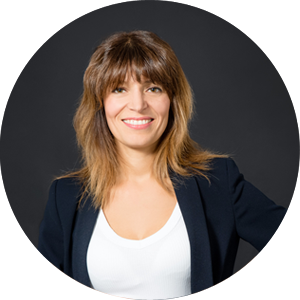
Booster la carrière des cadres et managers d’entreprise, aider les dirigeants à faire croître leur chiffre d’affaires et leur leadership, soutenir le lancement des futurs chefs d’entreprise, telle est la mission que j’ai donnée à Egidea Formation lors de sa création.
Parce que la mise en confiance et la valorisation des individus sont les clés de la réussite, parce que l’anticipation, la préparation et le travail sont les conditions du succès des entreprises et parce que l’expertise génère la confiance auprès des clients, la formation occupe plus que jamais une place centrale dans l’entreprise aussi bien que dans le parcours professionnel de chacun.
C’est la raison pour laquelle, chez Egidea Formation, nous mettons tout en œuvre pour vous proposer des formations de haute qualité qui prennent en compte vos attentes : définition de vos besoins personnels, montage de votre dossier de financement, parcours sur-mesure, planning personnalisé, outils pédagogiques variés, formateurs sélectionnés et formés selon nos méthodes, et bien d’autres caractéristiques qui rendent nos formations plus percutantes et surtout plus utiles.
Chez Egidea, la qualité n’est pas une option, la formation non plus.
Delphine Minassian
Directrice & Fondatrice d’Egidea
Nos points forts
pas d'attente !
Entrez en formation
au moment où vous en avez besoin
effectifs réduits
2 à 8 participants
maximum
Personnalisation
Personnalisez votre formation
en y ajoutant les options de votre choix
Ils nous font confiance
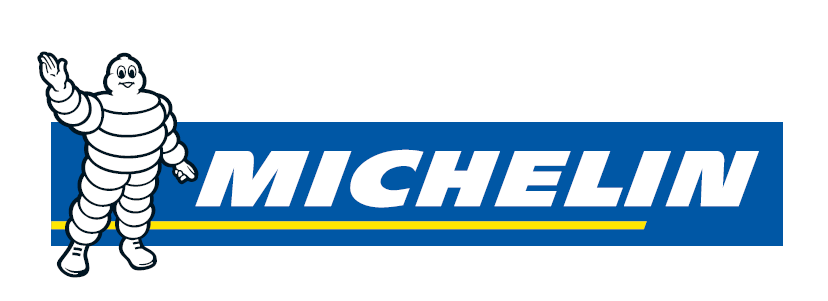
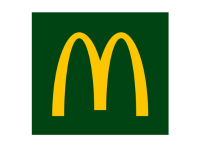
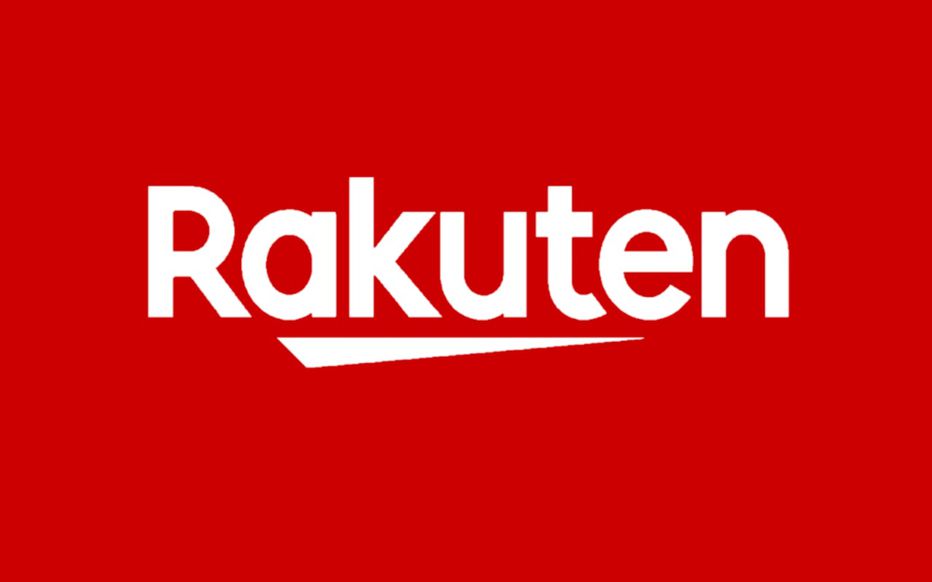
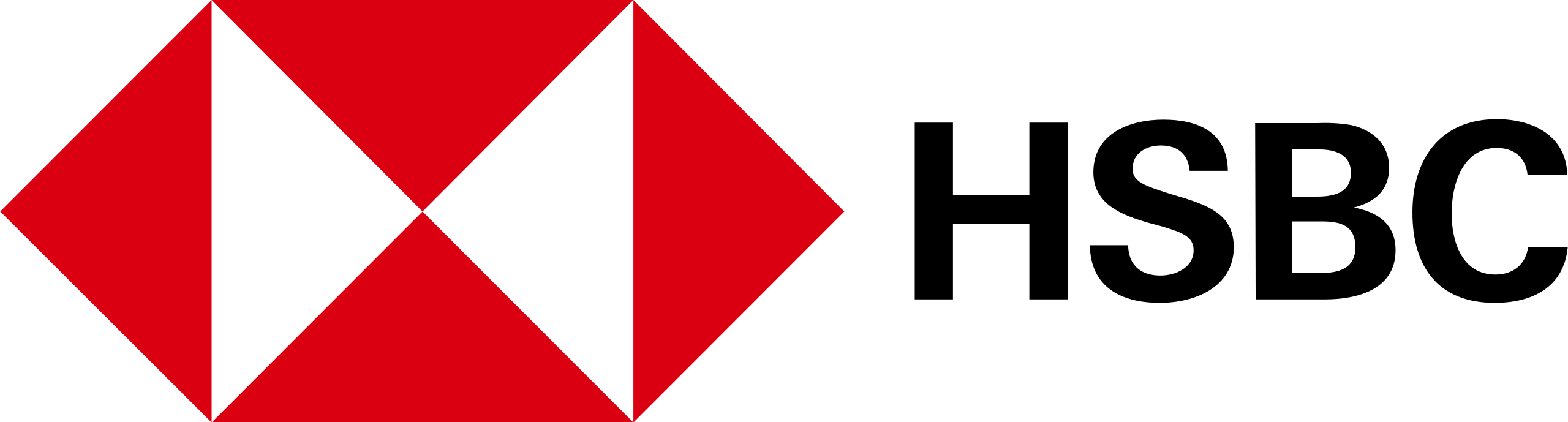

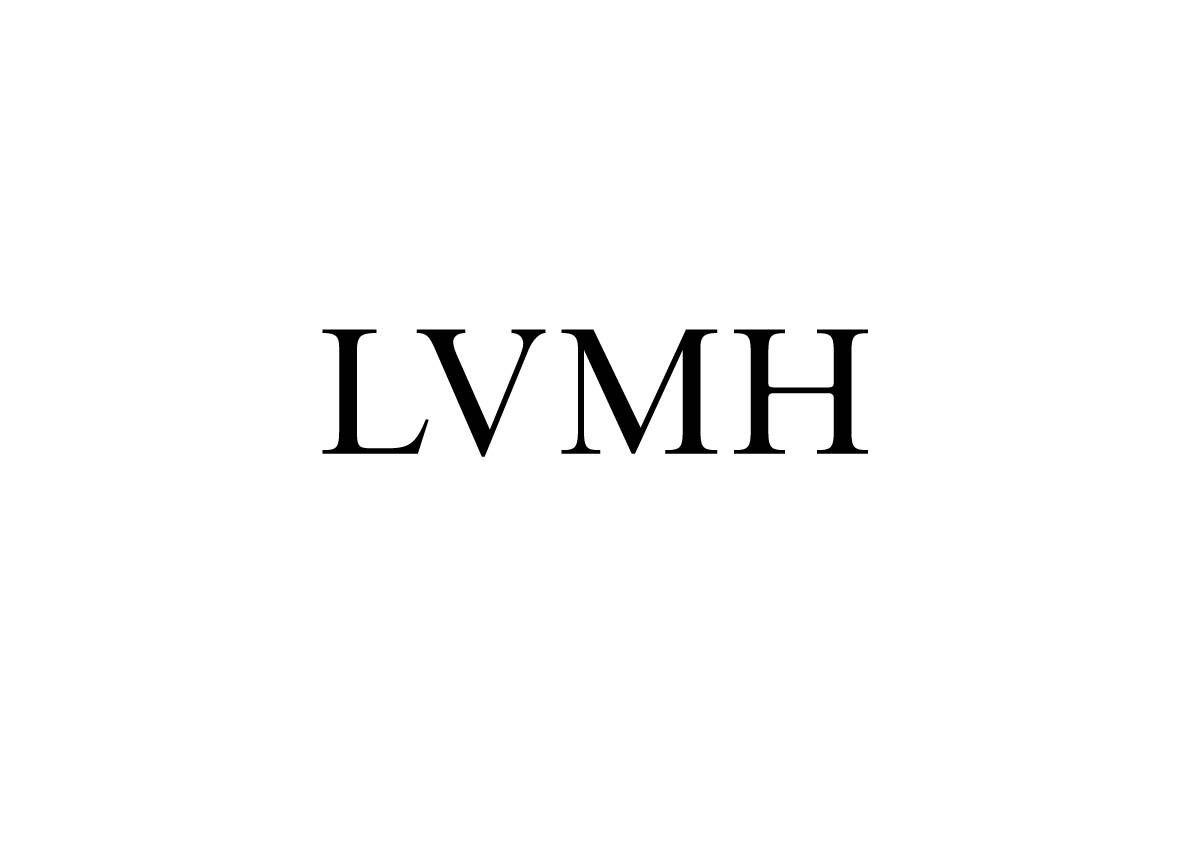
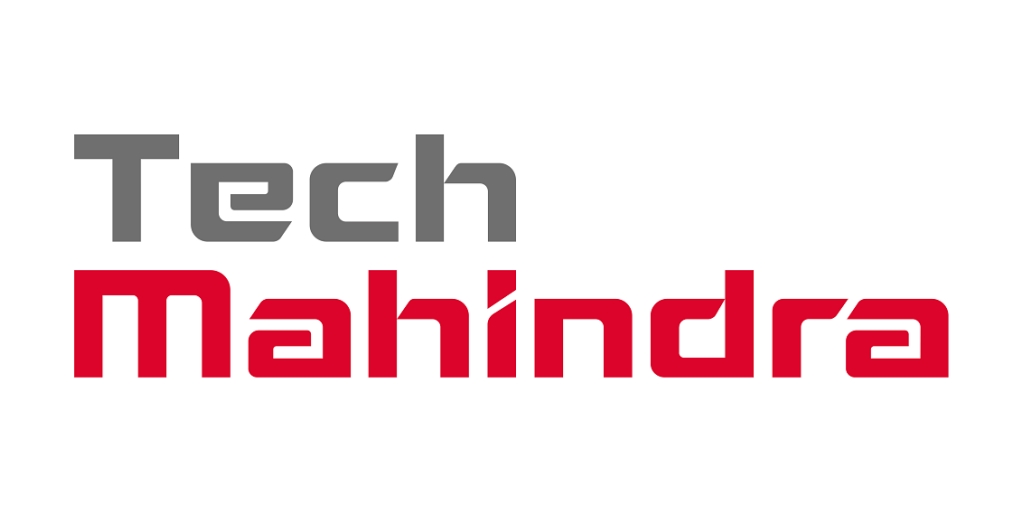
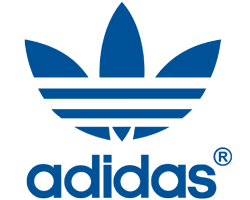
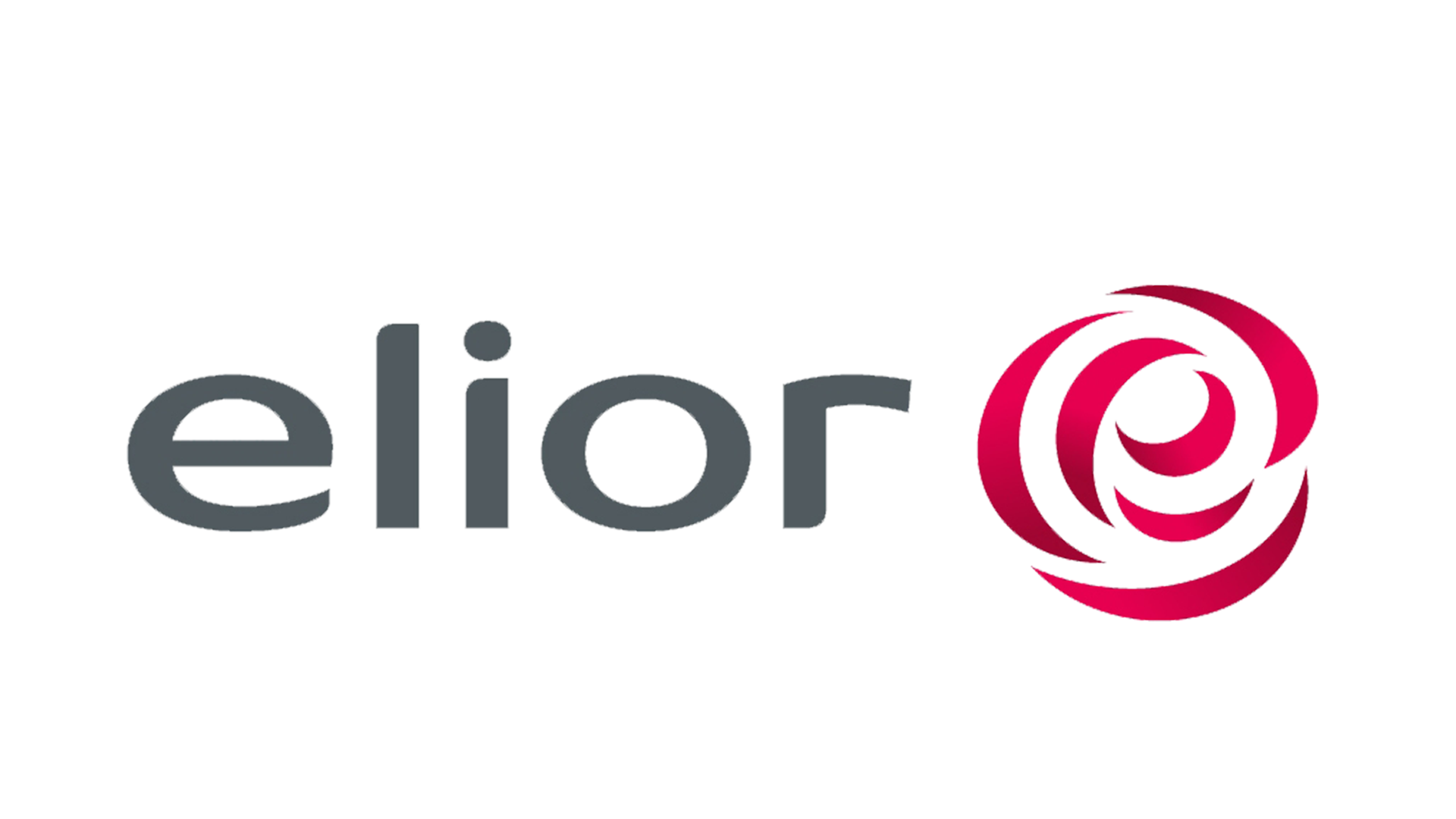
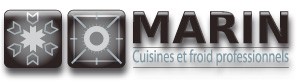
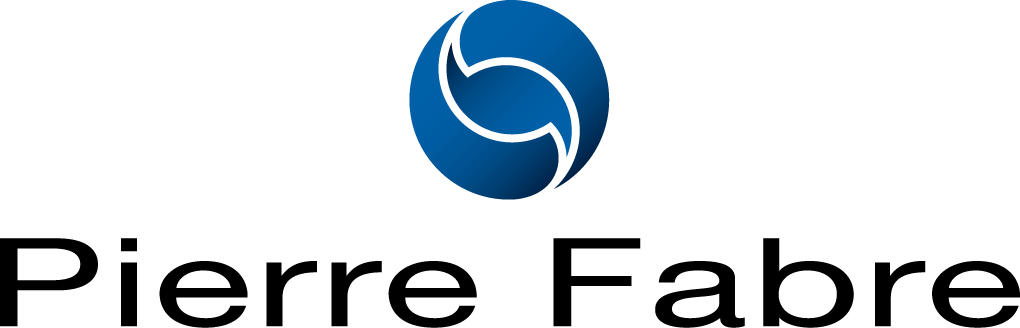
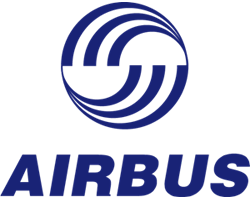
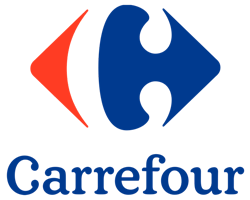
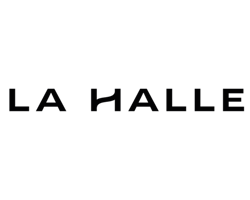
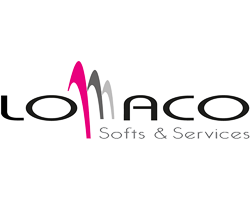
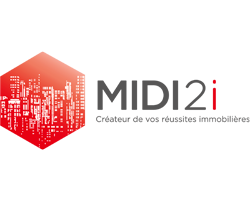
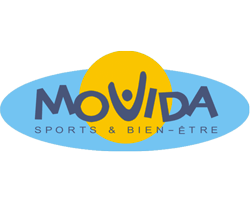
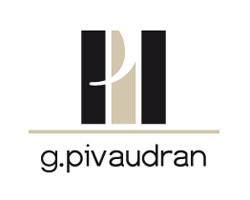
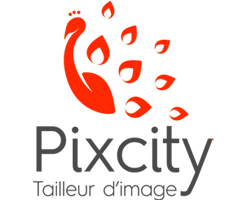
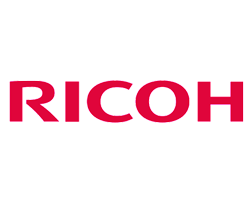
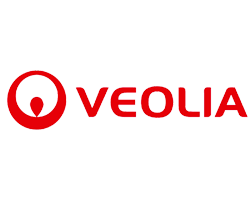
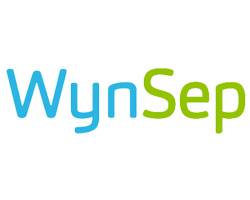